Freedom Celebrates 5 Years of Improving Manufacturers’ Operational Growth
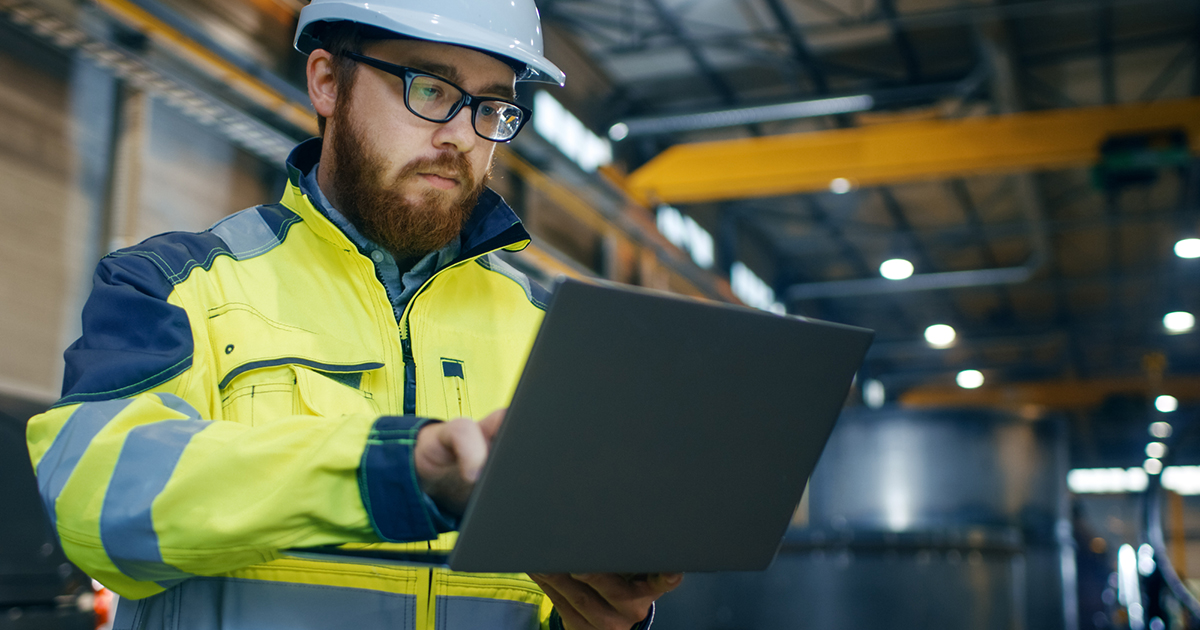
An increasingly global manufacturing marketplace continues to expand the competitive borders of the manufacturing environment. At the same time, tighter margins, smaller lot sizes, and higher quality requirements demand advanced technical solutions that help organizations achieve lean manufacturing across each stage of the production cycle. Since 2013, 5ME LLC has provided manufacturers with a web-based software suite that does just that. FREEDOM™ Smart Manufacturing platform delivers real-time collection and analysis of important manufacturing data that is accessible on any web browser and any device, connecting every asset on the shop floor and providing analytics to its users everywhere from the shop floor to the top floor.
Smart Manufacturing, IoT, and IIoT: What Publications You Should Read to Keep Your Competitive Edge

There’s an influx of information on the internet about smart manufacturing, IoT, and IIoT that makes it difficult to know what publications to pay attention to. At FREEDOM™, we know smart manufacturing – with our Smart Manufacturing Platform we stay up-to-date on industry trends, insights, and publications around these topics. Here are five articles we gathered to help keep your competitive edge.
The Difference between Home-Grown Solutions and Smart Manufacturing Technology
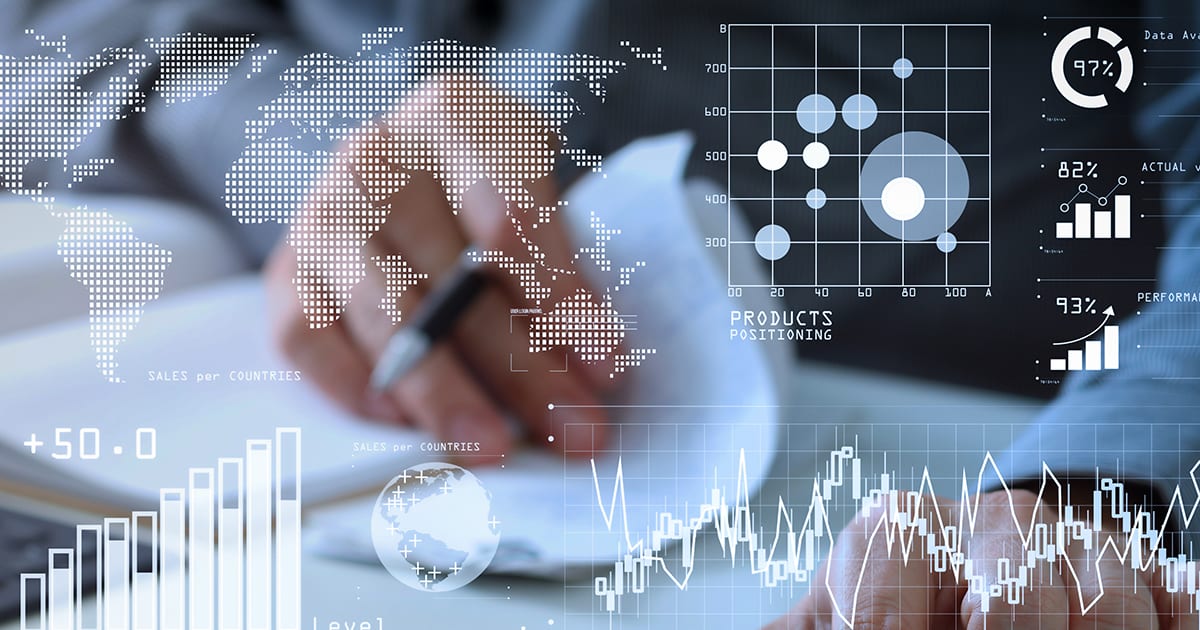
An operating platform is a foundation to manufacturer’s entire infrastructure. Depending on what systems are in place, these applications work together by sharing data which give manufacturers real-time visibility that enables instant decision-making. So, what’s holding manufacturers back from implementing smart manufacturing technology? Let’s take a look.
Why Smart Manufacturing and Improving OEE Must Go Hand in Hand
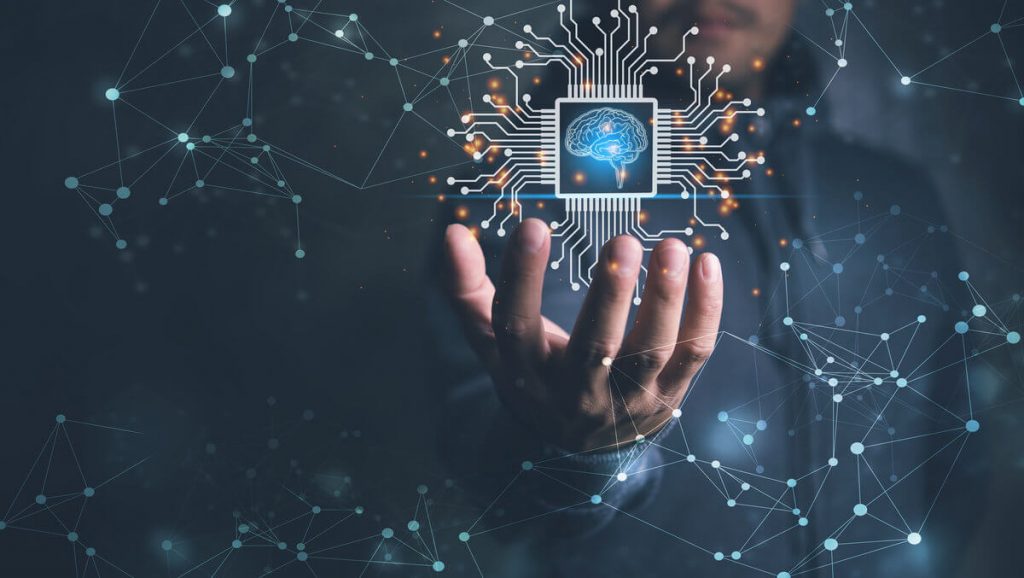
Smart manufacturing strategies and solutions are helping organizations across sectors stay competitive in today’s rapidly evolving marketplace. Digital, Industrial Internet of Things (IIoT) technologies are simplifying real-time collection and analysis of essential manufacturing data, information that is helping to boost productivity, improve product quality and enhance operational agility across the value stream.
Why Today’s Manufacturers Must Invest in Smart Manufacturing
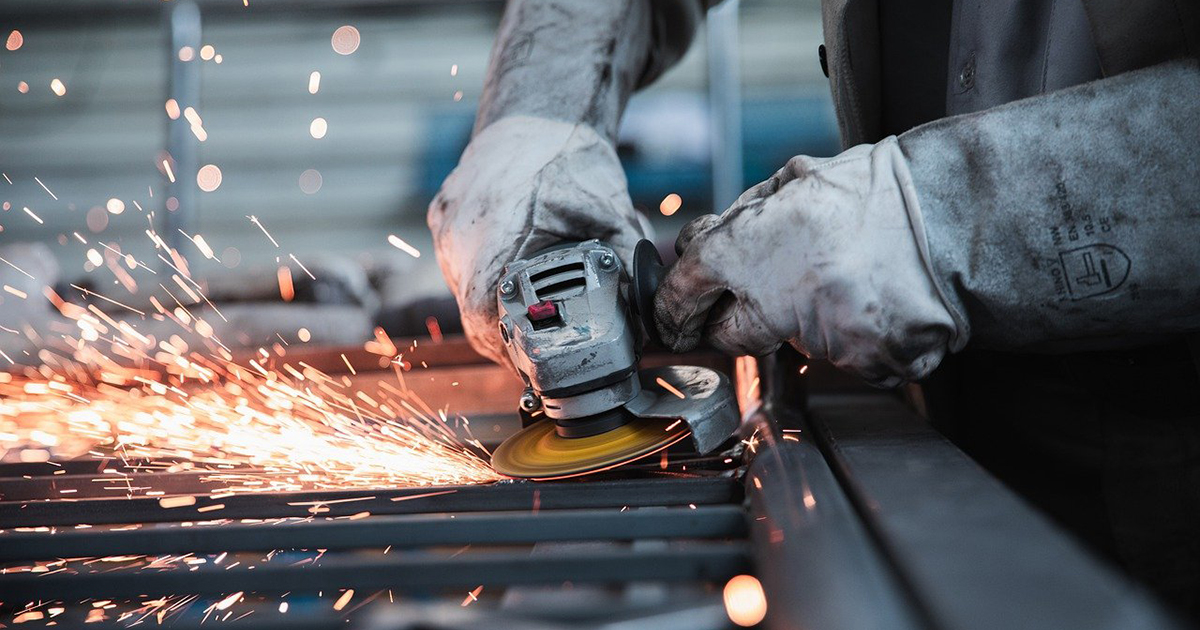
Smart manufacturing is a growing trend that shows no signs of stopping. Across industries, digital technologies and Industrial Internet of Things (IIoT) solutions are transforming the shop floor from traditional linear operations to interconnected systems that communicate, adapt, collect, exchange and analyze data. These solutions are helping organizations boost production, improve efficiency and increase cost-savings, while simultaneously reducing unplanned downtime, part setup time, required system maintenance, and more.
How to Improve OEE with Smart Manufacturing Technologies
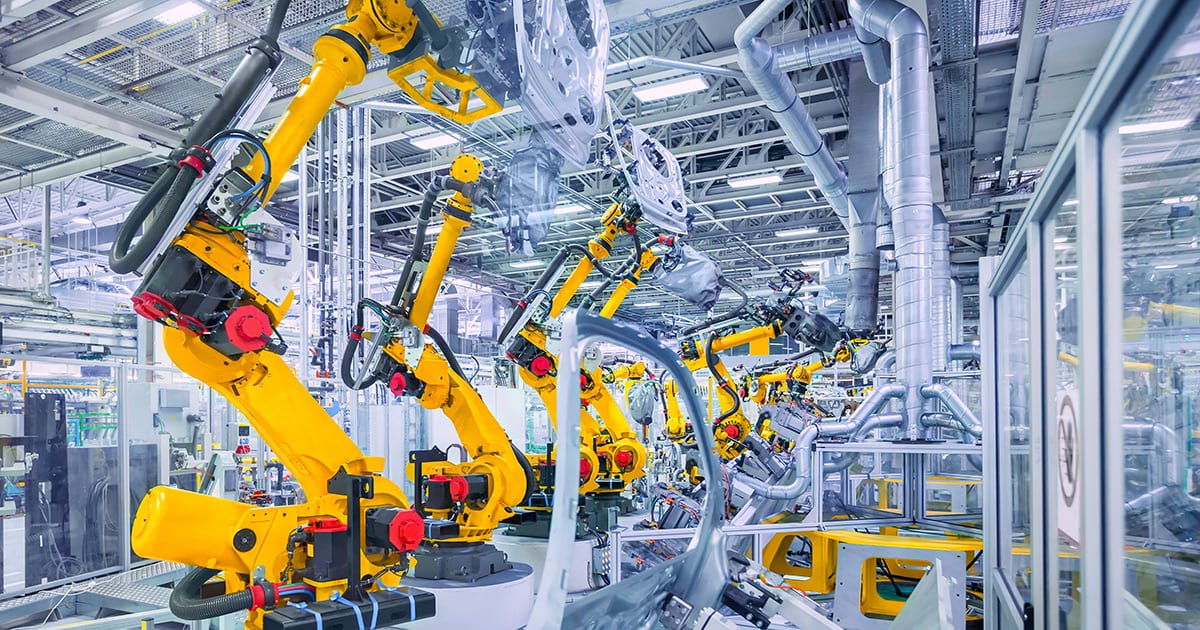
The National Institute of Standards and Technology (NIST) defines “smart manufacturing” as “fully-integrated, collaborative manufacturing systems that respond in real time to meet changing demands and conditions in the factory, in the supply network, and in customer needs.” In short, smart manufacturing is the optimization of every aspect of the value stream via interconnected solutions that facilitate automation, real-time monitoring, and continuous data analysis to increase efficiency and productivity.
Advanced Technologies and the North American Manufacturing Landscape
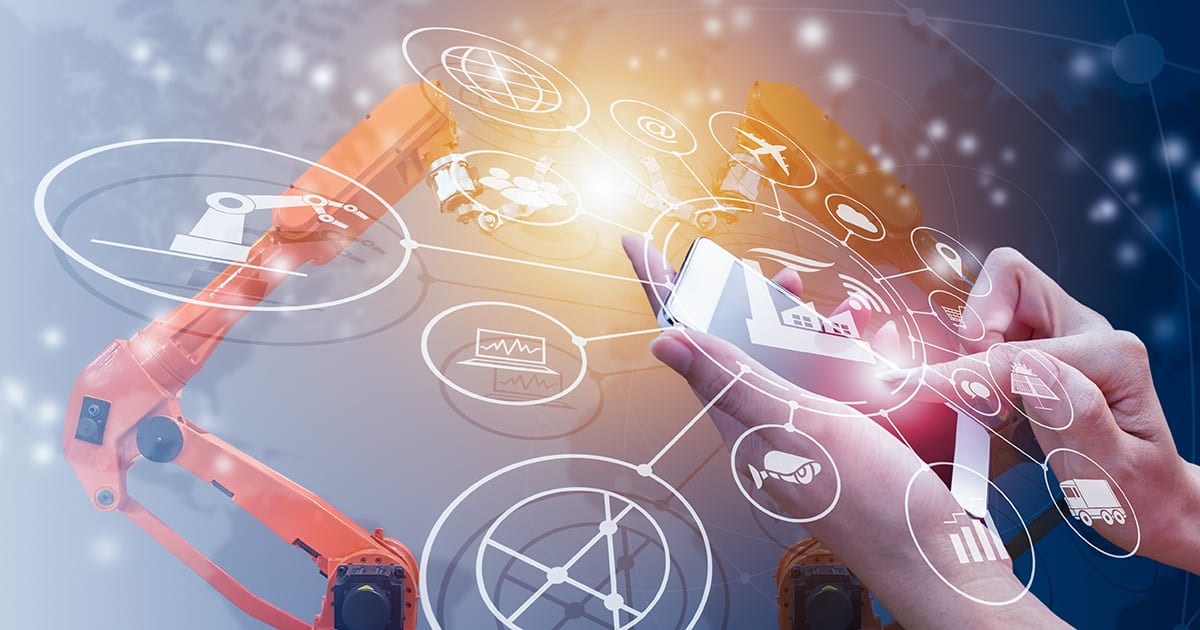
The technology landscape for North American manufacturers continues to grow more complex as new automated, smart technologies are introduced at a rapid pace. Automated, smart technologies are helping manufacturers keep step with this fluctuating marketplace, enabling them to maximize cost, delivery, flexibility, and quality via interconnected solutions that promote rapid flow and widespread use of digital information within and between manufacturing systems.
What we learned at IMTS 2018
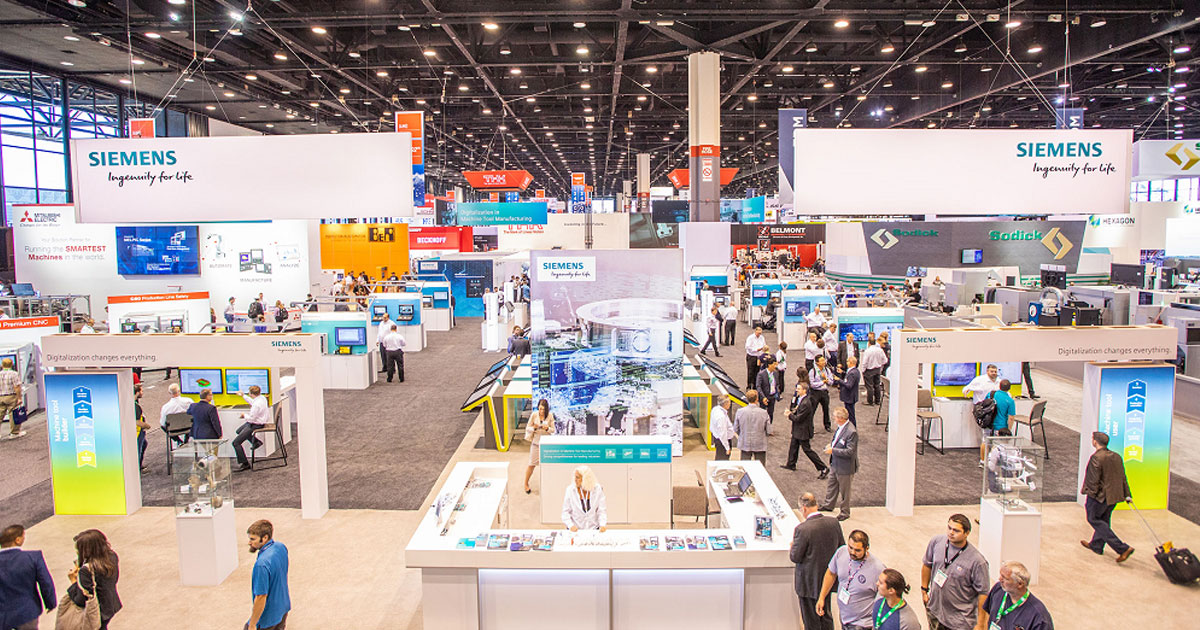
FREEDOM™ demonstrated its growing, connected IIoT Smart Manufacturing Platform at IMTS 2018. More than 2,500 manufacturers brought their latest and greatest technologies to Chicago, Illinois. It was a record-breaking year for registrations, square feet of exhibit space, exhibiting companies, and booths.
How Smart Manufacturing Software Benefits the Medical Manufacturing Sector
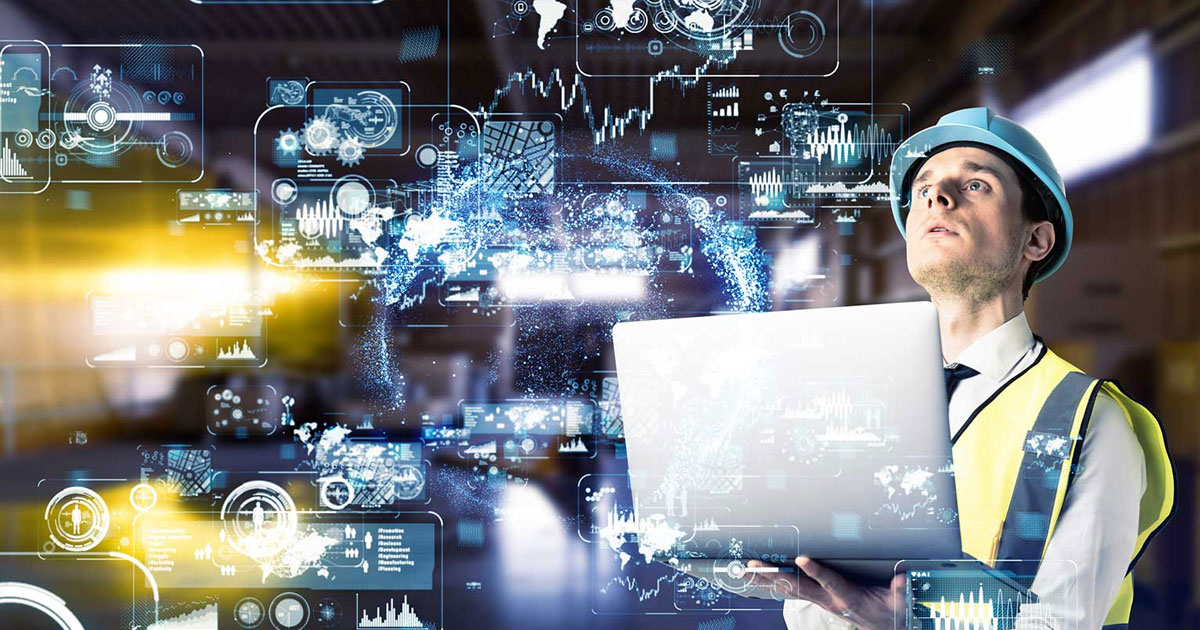
The competitive and highly regulated medical sector is one of the fastest growing segments of today’s manufacturing marketplace. This rapid growth requires smart management—of assets, budgets, processes and more.
How Smart Manufacturing Software Can Improve Efficiency
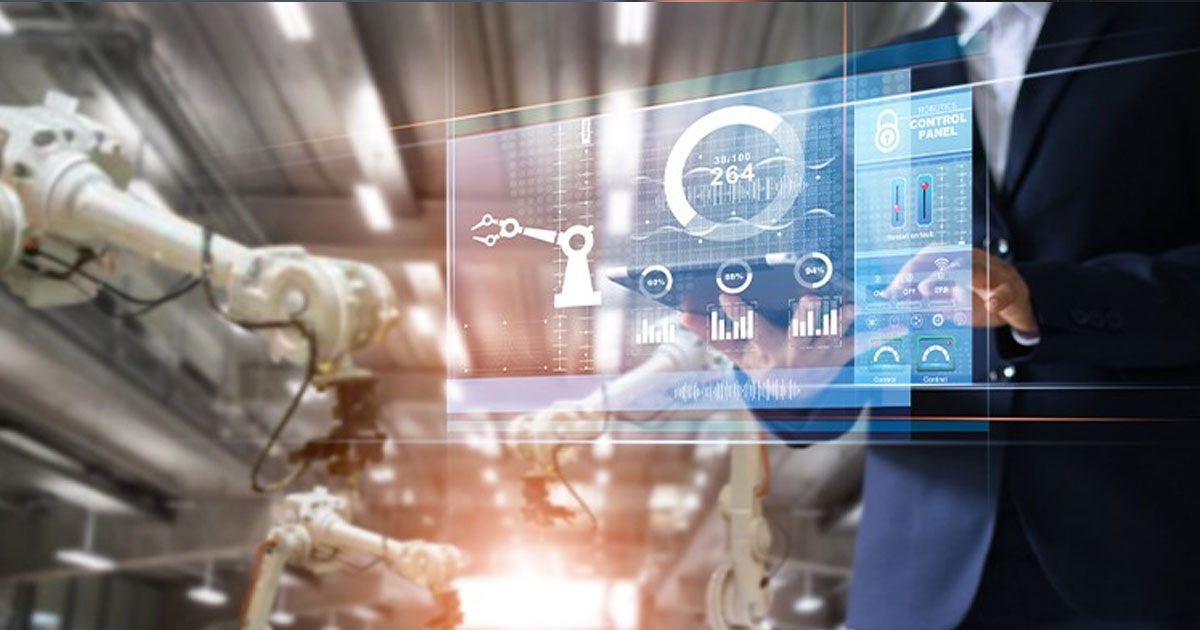
To thrive in today’s competitive manufacturing environment, you need to ensure optimal performance of assets while continuously increasing efficiency and reducing costs.
To improve processes, you must be able to measure in real-time what is working and what isn’t. Outdated data or a lack of current data can add to a growing performance problem, putting productivity, efficiency, and profitability at risk.
Your factory floor is an excellent example of where you should be continually capturing and analyzing data.